12 Must-Know Facts About Automatic Glass Grinding Machines
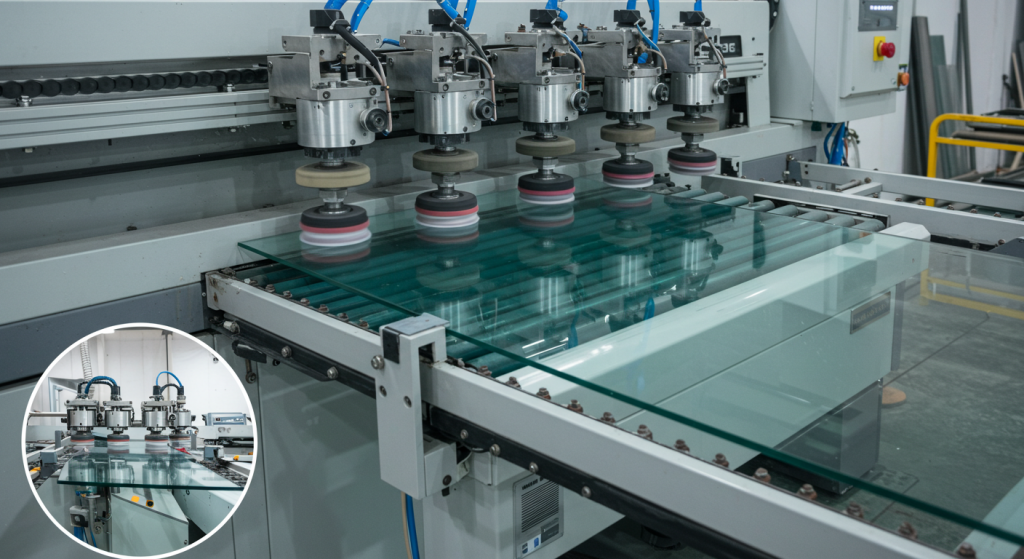
Automatic glass grinding machines are cutting-edge CNC tools designed to grind and smooth the edges or surfaces of glass panels with unparalleled precision and efficiency. These machines are pivotal in industries like architecture, automotive, furniture, and electronics, where flawless glass finishes are critical for safety, aesthetics, and functionality. By automating the grinding process, they eliminate the inconsistencies of manual methods, delivering uniform results that meet stringent industry standards.
Fujian Baineng CNC Equipment Co., Ltd. is a global leader in glass processing technology, offering innovative automatic glass grinding machines that combine advanced features with robust design. These machines cater to diverse production needs, from small-scale artisanal projects to high-volume industrial applications. Equipped with diamond or resin-bonded grinding wheels, CNC controls, and efficient cooling systems, Baineng’s solutions ensure high-quality finishes on glass ranging from 3mm to 25mm thick. This guide explores 12 must-know facts about these machines, providing a comprehensive look at their technology, applications, and why Baineng stands out.
The Evolution of Glass Grinding Technology
Glass grinding has evolved significantly over the decades. Early methods relied on manual tools and abrasive stones, which were slow, labor-intensive, and inconsistent. The introduction of mechanized grinding in the 20th century improved efficiency, but it was the advent of CNC technology that revolutionized the industry. Automatic glass grinding machines now integrate digital controls, multi-wheel systems, and real-time sensors, enabling precise, high-speed processing.
Fujian Baineng has been at the forefront of this evolution, incorporating innovations like automated wheel adjustments and energy-efficient designs. Their machines reflect decades of technological advancements, offering manufacturers the ability to produce complex edge profiles with minimal effort. This evolution has made automatic glass grinding machines indispensable for modern production, ensuring manufacturers can meet the growing demand for high-quality glass products.
How Automatic Glass Grinding Machines Operate
The operation of an automatic glass grinding machine is a sophisticated, multi-stage process:
- Setup: Glass panels are loaded onto a worktable or conveyor, secured to prevent movement.
- Grinding: Diamond or resin-bonded wheels grind the edges or surfaces, removing imperfections and shaping the glass to the desired profile.
- Cooling: A water-based coolant system dissipates heat, protecting the glass and extending wheel life.
- Finishing: Fine grinding wheels smooth the surface, preparing it for polishing or subsequent processing.
Baineng’s machines feature advanced CNC systems that allow operators to program precise grinding parameters, such as wheel speed, pressure, and path. Real-time sensors monitor glass thickness and adjust settings dynamically, ensuring consistency across batches. This automated workflow minimizes human error, making these machines ideal for producing uniform edges on architectural panels, furniture glass, or electronic displays.
Advanced Features of Baineng’s Machines )
Fujian Baineng’s automatic glass grinding machines are packed with features that cater to modern manufacturing needs:
- Multi-Wheel System: Up to eight grinding wheels operate simultaneously, handling coarse and fine grinding in one pass, reducing cycle times.
- Precision CNC Controls: Programmable systems ensure accuracy within ±0.1mm, ideal for intricate edge profiles and complex designs.
- Versatile Processing Range: Capable of grinding glass from 3mm to 25mm thick, these machines suit applications from delicate decor to heavy-duty panels.
- Energy-Efficient Design: High-efficiency motors and optimized cooling systems reduce power and water consumption, lowering operational costs.
- Durable Construction: Stainless steel frames and corrosion-resistant components ensure longevity in harsh industrial environments.
- Intuitive Interface: Touchscreen controls with real-time diagnostics simplify operation, enabling operators to monitor and adjust settings effortlessly.
- Automated Adjustments: Sensors detect glass properties and adjust wheel pressure, ensuring consistent results without manual intervention.
These features make Baineng’s machines a top choice for manufacturers seeking to enhance productivity and quality.
Architectural Applications: Enhancing Building Design
Automatic glass grinding machines are critical in architecture, producing polished edges for windows, facades, and glass doors:
- Safety Compliance: Smooth edges eliminate sharp hazards, meeting strict building codes.
- Aesthetic Appeal: Uniform finishes enhance the visual sophistication of glass structures.
- Structural Integrity: Precise grinding ensures proper fitting for hardware and seals.
Case Study: A Singapore commercial complex used Baineng’s machines to grind edges for thousands of facade panels. The flawless finishes contributed to the building’s modern aesthetic, earning accolades from developers and architects.
Baineng’s machines excel in processing large panels, making them a preferred solution for architectural projects requiring scale, precision, and consistency.
Furniture and Interior Design: Crafting Premium Products
In furniture and interior design, automatic glass grinding machines create smooth edges for tabletops, shelves, partitions, and decorative panels:
- User Safety: Polished edges prevent injuries, critical for consumer-facing products.
- Design Excellence: Sleek finishes elevate the aesthetic of glass furniture, appealing to premium markets.
- Production Efficiency: Automation enables high output to meet market demand.
Case Study: A Spanish furniture manufacturer boosted production by 40% using Baineng’s machines, producing polished glass tabletops that became a bestseller in luxury retail.
These machines empower designers to deliver high-quality, safe, and visually stunning glass products.
Automotive Glass: Precision for Safety and Fit
Automotive glass, including windshields, side windows, and mirrors, requires precise grinding to ensure proper fit and safety:
- Accurate Fitting: Ground edges align perfectly with vehicle frames, ensuring secure installation.
- Enhanced Durability: Smooth edges reduce stress points, improving glass strength.
- High Throughput: Automation meets the automotive industry’s tight production schedules.
Case Study: A Japanese supplier reduced edge defects by 25% with Baineng’s machines, enhancing windshield reliability for high-performance vehicles.
Baineng’s machines are tailored to the automotive sector’s rigorous standards, delivering consistent, high-quality results.
Electronics Industry: Precision for High-Tech Glass
Glass used in smartphone screens, tablets, and monitors requires meticulous grinding to meet tight tolerances:
- Optical Clarity: Smooth edges enhance display performance and visual quality.
- Structural Integrity: Grinding eliminates micro-cracks, increasing screen durability.
- Precision Processing: Accurate grinding supports complex component integration.
Case Study: A Taiwanese electronics firm improved screen quality by 20% using Baineng’s machines, reducing defects in smartphone glass panels and boosting customer satisfaction.
These machines are essential for meeting the electronics industry’s high-tech requirements.
Comparing Automatic Glass Grinding Machines to Alternatives
Automatic glass grinding machines offer distinct advantages over other processing methods:
- Vs. Manual Grinding: Automatic machines provide unmatched speed, precision, and scalability, while manual grinding is slow, inconsistent, and suitable only for small, custom projects.
- Vs. Edging Machines: Grinding machines focus on surface and edge smoothing, preparing glass for further processing, while edging machines prioritize edge shaping (e.g., beveling or mitering). Both are complementary in fabrication workflows.
- Vs. Polishing Machines: Grinding machines remove material and shape surfaces, setting the stage for polishing machines to add a glossy finish. Grinding is a foundational step in achieving polished results.
- Vs. Cutting Machines: Grinding refines edges or surfaces after cutting shapes the glass. The two processes work in tandem to produce finished panels.
Key Strengths: Automatic glass grinding machines excel in high-volume production, precision automation, and versatility for straight or curved edges. Fujian Baineng’s machines optimize these strengths, offering reliable solutions for complex grinding tasks across industries.
Maintenance Best Practices for Optimal Performance
Proper maintenance is crucial for ensuring the longevity and performance of automatic glass grinding machines. Here are key practices:
- Daily Cleaning: Remove glass dust, coolant residue, and debris from wheels, conveyors, and worktables to prevent wear and maintain efficiency.
- Wheel Inspections: Regularly check grinding wheels for wear or damage. Replace worn wheels to ensure consistent edge quality and avoid defects.
- Cooling System Maintenance: Monitor coolant levels and flow to prevent overheating, which can damage glass or wheels. Clean filters and check for leaks.
- CNC System Calibration: Update software and calibrate CNC controls to maintain precision. Regular updates ensure compatibility with new features.
- Lubrication: Apply appropriate lubricants to moving parts like spindles and conveyors to reduce friction and extend component life.
- Baineng Support: Leverage Fujian Baineng’s global service network for expert troubleshooting, training, and rapid maintenance support to minimize downtime.
By following these practices, manufacturers can maximize machine lifespan and sustain high production standards.
Benefits of Investing in Automatic Glass Grinding Machines
Investing in automatic glass grinding machines offers numerous advantages for manufacturers:
- Superior Precision: CNC automation ensures accurate grinding, meeting tight industry tolerances.
- Increased Efficiency: Single-pass processing reduces cycle times, enabling higher output and faster delivery.
- Versatility: Capable of processing various glass types, thicknesses, and edge profiles, these machines adapt to diverse applications.
- Cost Savings: Automation minimizes labor costs, reduces material waste, and lowers energy consumption, improving profitability.
- Consistent Quality: Uniform results enhance product reliability and market competitiveness.
- Scalability: Designed for high-volume production, these machines support business growth without compromising quality.
Fujian Baineng’s machines amplify these benefits with innovative features, robust construction, and energy-efficient designs, delivering exceptional value to glass processing professionals.
Future Trends Shaping Glass Grinding Technology
The glass grinding industry is poised for transformative advancements driven by technology and market demands:
- AI and Automation: Smart systems with AI integration will optimize grinding parameters, predict maintenance needs, and enhance precision through real-time data analysis.
- Sustainability: Eco-friendly designs, including energy-efficient motors and recyclable coolants, will reduce environmental impact and align with global sustainability goals.
- Customization: Machines will offer greater flexibility to handle complex edge profiles and bespoke designs, catering to niche markets and custom projects.
- Compact Solutions: Smaller, more affordable machines will emerge, making advanced grinding technology accessible to artisanal workshops and smaller manufacturers.
- IoT Integration: Internet of Things (IoT) connectivity will enable remote monitoring and diagnostics, improving uptime and operational efficiency.
Fujian Baineng is already pioneering these trends, developing next-generation machines that anticipate the industry’s future needs. Their proactive approach ensures manufacturers can stay competitive in a rapidly evolving market.
Conclusion
Automatic glass grinding machines are indispensable for achieving precise, efficient edge and surface finishing in industries like architecture, automotive, furniture, and electronics. Fujian Baineng’s innovative solutions deliver unmatched quality, speed, and versatility, empowering manufacturers to excel in competitive markets. From skyscraper facades to smartphone displays, these machines provide a strategic advantage. Visit bnmachine to explore Baineng’s offerings or contact their expert team for a tailored consultation. Invest in Baineng today and elevate your glass grinding operations to new heights.