Automatic Glass Drilling Machines: Precision Tools for Glass Fabrication
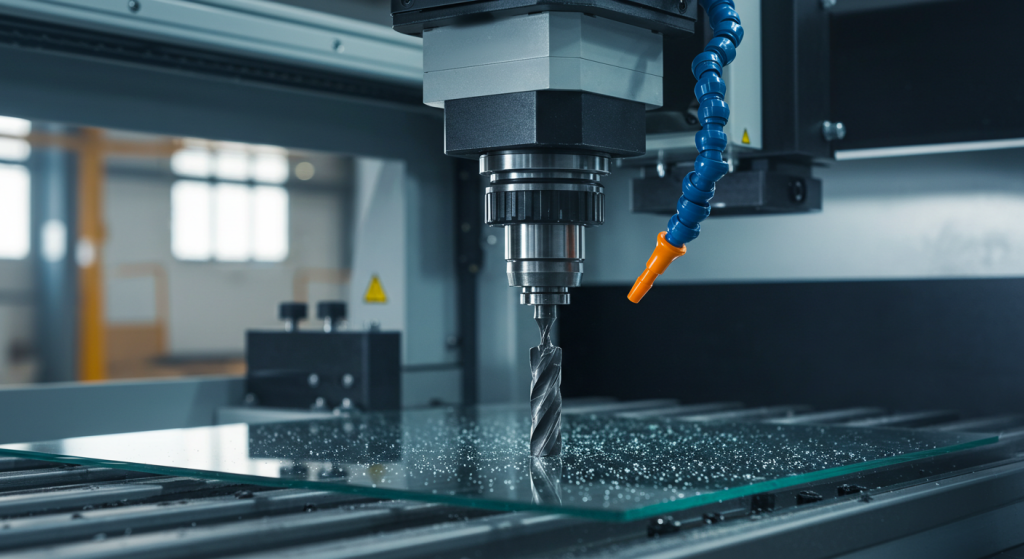
Precision is the cornerstone of modern glass manufacturing, and creating accurate, clean holes in glass panels is a critical task for many applications. Automatic glass drilling machines are state-of-the-art CNC-driven tools designed to drill holes with exceptional accuracy, speed, and consistency, eliminating the limitations of manual methods. These machines are indispensable in industries such as architecture, automotive, furniture, and electronics, where holes are needed for fittings, mounts, decorative elements, or structural components. By automating the drilling process, these systems enhance productivity, reduce errors, and ensure high-quality results that meet stringent industry standards.
Fujian Baineng CNC Equipment Co., Ltd. is a global leader in glass processing technology, renowned for its innovative and reliable automatic glass drilling machines. With a commitment to advancing manufacturing through cutting-edge solutions, Baineng caters to a wide range of production needs, from small-scale artisanal workshops to large industrial facilities. This comprehensive guide explores the technology, features, applications, and benefits of automatic glass drilling machines, highlighting why they are essential and how Baineng sets the benchmark for precision and efficiency.
Understanding Automatic Glass Drilling Machines
Definition and Purpose
An automatic glass drilling machine is a CNC-controlled system engineered to create precise holes in glass panels with minimal operator intervention. Using diamond-tipped drill bits, these machines produce clean, chip-free holes for applications such as hardware fittings, decorative patterns, or structural mounts. Designed for high-volume production, they deliver consistent results, making them ideal for industries requiring accuracy and scalability.
Core Components
Automatic glass drilling machines are built with several key components that ensure optimal performance:
- Drill Heads: Single or dual diamond-tipped drill bits operate from one or both sides of the glass, ensuring clean holes without chipping. Dual-sided drilling enhances efficiency and quality.
- Worktable: A stable, adjustable platform secures glass panels, accommodating sizes from small sheets to large panels and thicknesses from 3mm to 20mm.
- CNC Control System: Advanced interfaces allow operators to program hole size (4mm to 100mm), position, and depth with precision, ensuring repeatability across batches.
- Cooling System: Water or coolant is applied to the drilling area to reduce heat, prevent glass cracking, and extend drill bit lifespan, while also minimizing dust.
- Frame and Structure: Robust stainless steel construction provides stability during high-speed operations, ensuring durability in industrial environments.
Operational Process
The drilling process is streamlined and efficient:
- Positioning: The CNC system aligns drill heads with programmed coordinates, ensuring exact hole placement.
- Drilling: Diamond bits penetrate the glass, often from both sides simultaneously to prevent chipping and ensure a clean finish.
- Cooling: Coolant is applied continuously to manage heat and debris, maintaining glass integrity and hole quality.
This automated workflow adapts to various glass types, including tempered, laminated, and float, making these machines highly versatile for diverse manufacturing needs.
Technical Features of Automatic Glass Drilling Machines
Fujian Baineng’s automatic glass drilling machines are engineered for precision, efficiency, and durability, incorporating advanced features that set them apart in the industry:
- Dual-Sided Drilling Capability: Dual drill heads operate simultaneously from both sides of the glass, reducing processing time and ensuring chip-free holes. This feature is critical for high-volume production and high-quality finishes.
- High-Precision CNC Controls: Baineng’s machines feature CNC systems that allow programming of hole diameters, depths, and positions with an accuracy of ±0.1mm. Real-time sensors adjust drilling parameters based on glass properties, minimizing errors and enhancing consistency.
- Versatile Processing Range: Capable of drilling glass from 3mm to 20mm thick, these machines handle a wide range of applications, from thin decorative panels to thick structural glass. They support hole sizes from 4mm to 100mm, accommodating diverse project requirements.
- Automated Tool Changing: Advanced models include automatic tool changers, enabling seamless transitions between drill bit sizes without manual intervention, which boosts productivity and reduces downtime.
- Robust Construction: Built with stainless steel frames and corrosion-resistant components, Baineng’s machines withstand the demands of continuous industrial use, ensuring long-term reliability with minimal maintenance.
- Energy Efficiency: High-efficiency motors and optimized cooling systems reduce power and water consumption, aligning with sustainable manufacturing practices and lowering operational costs.
- User-Friendly Interface: Touchscreen controls with real-time diagnostics simplify operation, providing intuitive access to programming and monitoring functions. This accessibility ensures operators of all skill levels can achieve precise results.
These technical advantages make Baineng’s automatic glass drilling machines a preferred choice for manufacturers seeking to optimize their glass fabrication processes while maintaining exceptional quality standards.
Applications Across Industries
Automatic glass drilling machines are versatile tools that serve a broad spectrum of industries, delivering precise holes for both functional and decorative purposes. Below are key applications, each supported by real-world examples:
Architectural Glass
In modern architecture, holes in glass panels are essential for fittings such as hinges, handles, or structural mounts in windows, doors, and curtain walls. Automatic drilling machines ensure accurate, clean holes that meet rigorous design and safety standards.
Case Study: A Hong Kong office tower project utilized Baineng’s automatic glass drilling machines to create precise holes for glass curtain walls. The accurate hardware alignment enhanced the building’s structural integrity and aesthetic appeal, earning praise from project managers.
Furniture and Interior Design
Glass furniture, such as tabletops, shelves, and cabinets, requires holes for mounting hardware or decorative elements. These machines deliver chip-free holes that enhance safety and elevate design quality.
Case Study: A French furniture designer increased production capacity by 40% using Baineng’s machines. The precisely drilled holes in glass cabinet panels met the high-end market’s demand for flawless craftsmanship, boosting brand reputation.
Automotive Glass
Holes in windshields, side windows, and mirrors are critical for sensors, mounting brackets, or rearview mirror attachments. Automatic drilling machines meet the automotive industry’s stringent requirements for precision and durability.
Case Study: An American automotive supplier reduced drilling errors by 22% with Baineng’s machines, improving the reliability of glass components for electric vehicles and streamlining production to meet tight schedules.
Electronics
Glass used in displays and touchscreens for smartphones, tablets, and monitors requires precise holes for buttons, connectors, or camera modules. Baineng’s machines provide the accuracy needed for high-tech applications.
Case Study: A Chinese electronics manufacturer enhanced display quality by 15% using Baineng’s equipment. The clean, precise holes reduced defects in smartphone glass panels, improving product performance and customer satisfaction.
These case studies underscore the transformative impact of automatic glass drilling machines across diverse, high-precision industries, demonstrating their ability to deliver consistent, high-quality results.
Comparison with Other Glass Processing Machines
To select the right equipment, manufacturers must understand how automatic glass drilling machines compare to alternatives:
- Automatic vs. Manual Drilling Machines: Automatic machines leverage CNC automation for superior speed, precision, and scalability, making them ideal for high-volume production. Manual drilling machines, while suitable for small, custom jobs, are slower, less accurate, and require significant operator skill, limiting their efficiency.
- Drilling vs. Edging Machines: Drilling machines focus on creating holes within glass panels, addressing internal features like fittings or mounts. Edging machines refine the perimeter of glass, producing smooth or beveled edges. Both are complementary in glass fabrication, with drilling often following edging in production workflows.
- Drilling vs. Cutting Machines: Drilling machines create holes within glass panels, while cutting machines shape the glass itself by creating panels or custom forms. Drilling is typically a secondary process, performed after cutting, to add functional or decorative features.
Key Strengths: Automatic glass drilling machines excel in precision, speed, and automation, making them indispensable for manufacturers requiring consistent, high-volume hole-making. Their ability to handle complex drilling patterns and adapt to various glass types enhances their versatility. Fujian Baineng’s machines optimize these strengths, offering reliable, high-performance solutions for intricate drilling tasks.
Maintenance and Troubleshooting Tips
Regular maintenance is essential to ensure the longevity and optimal performance of automatic glass drilling machines:
- Daily Cleaning: Remove glass dust, coolant residue, and debris from drill heads, worktables, and other components to prevent wear and maintain operational efficiency. Regular cleaning extends the life of critical parts.
- Drill Bit Inspections: Monitor diamond-tipped drill bits for wear or damage. Replace worn bits promptly to ensure clean, precise holes and avoid defects that could compromise product quality.
- Cooling System Checks: Verify coolant levels and flow daily to prevent overheating, which can crack glass or damage drill bits. Clean filters and check for leaks to ensure the cooling system operates effectively.
- Control System Calibration: Periodically calibrate CNC systems to maintain precision. Update software to access new features and ensure compatibility with evolving production needs, keeping the machine at peak performance.
- Baineng Support: Fujian Baineng’s global service network provides expert troubleshooting, operator training, and rapid maintenance support. Their responsive team minimizes downtime, ensuring continuous production and long-term reliability.
By adhering to these maintenance practices, manufacturers can maximize the lifespan of their automatic glass drilling machines and sustain high production standards.
Benefits of Automatic Glass Drilling Machines
Automatic glass drilling machines offer a range of compelling advantages for manufacturers:
- Unmatched Precision: CNC automation ensures accurate hole placement, size, and depth, meeting stringent industry standards and reducing defects.
- High Efficiency: Automated drilling significantly reduces cycle times, enabling faster production and higher output to meet tight deadlines.
- Versatility: Capable of processing various glass types, thicknesses, and hole sizes, these machines adapt to diverse manufacturing needs, from functional fittings to intricate designs.
- Cost Efficiency: By minimizing labor requirements, reducing errors, and optimizing resource use, these machines lower operational costs, improving profitability and sustainability.
- Scalability: Designed for high-volume production, they support manufacturers in scaling operations without compromising quality.
Fujian Baineng’s machines amplify these benefits with innovative technology, robust construction, and energy-efficient designs, delivering exceptional value to glass processing professionals.
Why Fujian Baineng Stands Out
Fujian Baineng CNC Equipment Co., Ltd. is a trusted global leader in glass processing solutions, distinguished by several key strengths:
- Innovation: Baineng’s machines incorporate cutting-edge CNC technology, ensuring precision, adaptability, and readiness for modern manufacturing challenges. Their ongoing R&D efforts drive continuous improvements, keeping them ahead of industry trends.
- Quality Assurance: Certified to CE and ISO standards, every Baineng machine undergoes rigorous testing to guarantee durability, performance, and safety. This commitment to quality provides customers with confidence in their investment.
- Global Support: With an extensive service network, Baineng offers comprehensive training, maintenance, and rapid-response support worldwide. Their customer-centric approach ensures long-term success and minimal operational disruptions.
- Customization: Baineng provides tailored solutions to address specific production needs, from small-scale artisanal projects to high-volume industrial applications, maximizing return on investment.
Baineng’s philosophy—“technology innovation, quality first, sharing and win-win, to be sincere forever”—underpins their commitment to building lasting partnerships and delivering unmatched value to glass manufacturers.
Future Trends in Glass Drilling Technology
The glass drilling industry is evolving rapidly, driven by technological advancements and market demands. Key trends include:
- AI and Automation: Smart systems with AI integration will optimize drilling performance, predict maintenance needs, and enhance precision through real-time data analysis, reducing downtime and improving efficiency.
- Sustainability: Eco-friendly designs, including energy-efficient motors and reduced coolant usage, will become standard, aligning with global sustainability goals and minimizing environmental impact.
- Customization: As demand for bespoke glass designs grows, machines will offer greater flexibility to handle complex hole patterns and specialized applications, catering to niche markets and custom projects.
- Compact Solutions: Smaller, more affordable drilling machines will emerge, making advanced technology accessible to smaller workshops and artisanal producers, democratizing precision drilling.
Fujian Baineng is already at the forefront of these trends, developing next-generation machines that anticipate the industry’s future needs. Their proactive approach ensures manufacturers can stay competitive in a rapidly changing market.
Conclusion
Automatic glass drilling machines are indispensable tools for achieving precise, efficient hole-making in industries such as architecture, automotive, furniture, and electronics. Their automation, precision, and versatility make them a strategic asset for manufacturers seeking to elevate their fabrication capabilities. Fujian Baineng CNC Equipment Co., Ltd. leads the industry with innovative, reliable, and customer-focused solutions that deliver exceptional quality and value. Whether you’re drilling holes for curtain walls, furniture fittings, or smartphone displays, Baineng’s machines provide a competitive edge. Visit bnmachine.com to explore their offerings or contact their expert team for a tailored consultation. Invest in Baineng today and transform your glass fabrication operations.