CNC Precision Manufacturing for Life Rafts, Propellers, Rudders, and Anchors
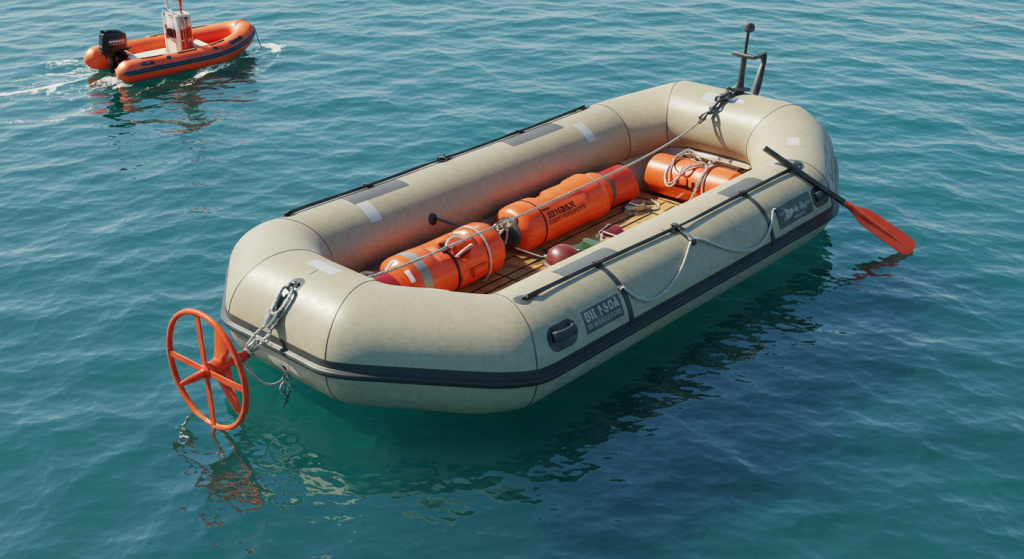
In the maritime industry, where safety, performance, and reliability are non-negotiable, precision manufacturing is the cornerstone of success. Components like life rafts, propellers, rudders, and anchors play critical roles in ensuring vessels operate efficiently and safely under the harshest conditions. A minor manufacturing defect can lead to increased fuel costs, compromised navigation, or even life-threatening failures. At BN Machine, we specialize in advanced Computer Numerical Control (CNC) machinery that delivers the precision and consistency maritime manufacturers need. This comprehensive guide explores how CNC technology revolutionizes the production of life rafts, propellers, rudders, and anchors, highlighting BN Machine’s cutting-edge solutions and their impact on the maritime industry.
The Critical Role of Precision in Maritime Manufacturing
Maritime components face relentless challenges: corrosive saltwater, extreme pressures, and constant mechanical stress. Whether it’s a propeller driving a cargo ship through turbulent seas or a life raft deploying in an emergency, every part must perform flawlessly. Precision manufacturing, powered by CNC machinery, ensures these components meet exacting standards, delivering durability, safety, and efficiency.
CNC machines—such as routers, milling machines, and vertical drilling systems—offer unparalleled accuracy by automating complex tasks. Unlike traditional manual methods, CNC technology eliminates human error, achieves tolerances as tight as 0.001 inches, and minimizes material waste. For maritime manufacturers, this translates to reduced production costs, enhanced vessel performance, and compliance with stringent regulations, such as those set by the International Maritime Organization (IMO) and the Safety of Life at Sea (SOLAS) convention.
At BN Machine, our state-of-the-art CNC solutions empower manufacturers to produce high-quality maritime components with speed and precision. Let’s examine how CNC machinery transforms the production of propellers, rudders, anchors, and life rafts, ensuring they meet the demands of modern maritime operations.
CNC Manufacturing for Propellers
The Importance of Propellers in Vessel Efficiency
Propellers are the driving force behind a vessel’s propulsion, converting engine power into thrust. A well-designed and precisely manufactured propeller optimizes fuel efficiency, reduces vibration, and enhances maneuverability. However, even a slight imperfection—such as an uneven blade surface or misaligned pitch—can lead to cavitation, increased noise, or reduced performance, costing operators thousands in fuel and maintenance.
CNC Milling and Routing for Propeller Production
CNC machinery, particularly 5-axis milling machines and CNC routers, is ideally suited for crafting propellers with complex, hydrodynamic shapes. These machines can process high-strength materials like stainless steel, bronze, aluminum, and nickel-aluminum alloys, which are commonly used in propeller manufacturing. The 5-axis capability allows simultaneous movement along multiple axes, enabling the creation of intricate blade contours without undercuts or seams.
The propeller manufacturing process with CNC technology typically involves:
- Design Phase: Engineers use Computer-Aided Design (CAD) software to create a 3D model of the propeller, optimizing blade shape, pitch, and diameter for specific vessel requirements.
- Programming: Computer-Aided Manufacturing (CAM) software translates the design into machine instructions, defining toolpaths for precision cutting.
- Machining: The CNC milling machine or router cuts the material, shaping each blade with micron-level accuracy and polishing surfaces to reduce drag.
- Quality Control: Automated inspection systems verify tolerances, ensuring the propeller meets design specifications.
BN Machine’s 5-axis CNC milling systems excel in producing propellers that achieve optimal hydrodynamic performance. For example, our machines can create blades with variable pitch designs, which improve thrust efficiency across a range of speeds.
Benefits of CNC Propeller Manufacturing
- Fuel Efficiency: Precise blade shaping reduces drag and cavitation, lowering fuel consumption by up to 10% in some cases.
- Consistency: CNC automation ensures every propeller matches the design, eliminating variability in production runs.
- Customization: Manufacturers can tailor propellers for specific vessels, from fishing boats to superyachts, using BN Machine’s versatile CNC systems.
- Durability: High-tolerance machining enhances resistance to wear and corrosion, extending propeller lifespan.
By leveraging BN Machine’s CNC solutions, manufacturers can produce propellers that not only enhance vessel performance but also contribute to significant operational cost savings.
CNC Manufacturing for Rudders
Rudders: Precision Steering for Safe Navigation
Rudders are essential for controlling a vessel’s direction, redirecting water flow to steer the ship. A rudder’s effectiveness depends on its hydrodynamic profile, surface finish, and structural integrity. Poorly manufactured rudders can cause sluggish steering, increased fuel consumption, or even structural failure under high loads, compromising safety.
CNC Precision for Rudder Production
CNC milling and routing are critical for shaping rudders, which often feature complex curves, tapered edges, and reinforced mounting points. BN Machine’s CNC routers, equipped with high-speed spindles and vacuum tables, can process materials like carbon fiber, stainless steel, and high-strength composites used in modern rudder designs. The manufacturing process includes:
- Design Optimization: Engineers create a 3D rudder model, optimizing its shape for minimal drag and maximum steering efficiency.
- Material Preparation: The material is secured on the CNC machine’s worktable, ensuring stability during high-speed cutting.
- Machining: The CNC router or milling machine shapes the rudder, following the digital design to achieve precise dimensions and smooth finishes.
- Secondary Operations: CNC systems drill mounting holes and add reinforcement features, preparing the rudder for assembly.
BN Machine’s CNC solutions support multi-axis machining, enabling the production of rudders with complex geometries, such as spade or skeg-supported designs. Our machines also ensure surface finishes that minimize turbulence, enhancing steering responsiveness.
Advantages of CNC Rudder Manufacturing
- Hydrodynamic Efficiency: Precise shaping reduces drag, improving fuel economy and steering precision.
- Structural Integrity: High-tolerance machining ensures rudders withstand mechanical stress and prolonged saltwater exposure.
- Scalability: CNC systems can produce rudders for vessels of all sizes, from small recreational boats to massive container ships.
With BN Machine’s CNC technology, manufacturers can deliver rudders that enhance vessel maneuverability, safety, and operational efficiency, meeting the needs of today’s maritime industry.
CNC Manufacturing for Anchors
Anchors: Ensuring Stability and Safety
Anchors are the foundation of a vessel’s stability, securing it during docking, storms, or emergencies. Manufacturing anchors requires precision to ensure they are strong, reliable, and capable of gripping various seabeds, from muddy bottoms to rocky surfaces. Components like flukes, shanks, and mounting holes must be machined with accuracy to guarantee performance and durability.
CNC Vertical Drilling for Anchor Production
CNC vertical drilling machines are essential for creating precise mounting holes and shaping anchor components. BN Machine’s vertical drilling systems offer high-speed, automated capabilities, ensuring holes are perfectly aligned and free of burrs. These machines can handle heavy-duty materials like cast iron, steel, and galvanized alloys, which are standard in anchor manufacturing.
The anchor production process typically involves:
- Drilling: CNC machines drill holes for bolts, chains, or shackles, ensuring exact placement and depth to withstand extreme loads.
- Milling: CNC milling machines shape the anchor’s flukes and shank, optimizing weight distribution and seabed penetration.
- Finishing: Automated polishing creates a smooth, corrosion-resistant surface, enhancing longevity in marine environments.
BN Machine’s CNC systems also support the production of specialized anchors, such as plow or claw designs, tailored to specific vessel types and operational needs.
Benefits of CNC Anchor Manufacturing
- Strength and Reliability: Precise drilling and milling create robust anchors that perform reliably under high loads.
- Corrosion Resistance: Automated finishing ensures smooth surfaces that resist rust and degradation.
- Cost Efficiency: CNC automation reduces labor costs and material waste, improving profitability for manufacturers.
BN Machine’s CNC drilling and milling solutions enable manufacturers to produce anchors that meet rigorous safety standards, ensuring vessels remain secure in any condition.
CNC Manufacturing for Life Rafts
Life Rafts: A Critical Safety Component
Life rafts are a vessel’s last line of defense in emergencies, designed to save lives during abandon-ship scenarios. Their construction requires lightweight, durable materials and precise assembly to ensure rapid deployment and resilience in harsh conditions. Components like frames, panels, and attachment points must be manufactured with accuracy to meet stringent safety regulations.
CNC Routing for Life Raft Components
CNC routers are ideal for cutting and shaping materials used in life rafts, such as composites, polymers, and aluminum. BN Machine’s CNC routers feature high-precision spindles, vacuum tables, and dust collection systems, ensuring clean cuts and safe material handling. The manufacturing process includes:
- Material Cutting: CNC routers cut panels, frames, and structural components to exact dimensions, minimizing weight while maintaining strength.
- Engraving: CNC systems engrave markings, serial numbers, or compliance labels for traceability and regulatory adherence.
- Assembly Preparation: Precise drilling and milling create attachment points for straps, valves, inflation systems, and other fittings.
BN Machine’s CNC routers support the production of both rigid and inflatable life rafts, accommodating a range of designs and materials.
Advantages of CNC Life Raft Manufacturing
- Lightweight Design: CNC routers optimize material use, reducing weight without compromising structural integrity.
- Safety Compliance: Precise manufacturing ensures life rafts meet IMO and SOLAS standards, guaranteeing reliability in emergencies.
- Production Speed: Automated cutting and assembly accelerate production, enabling manufacturers to meet tight delivery schedules.
By using BN Machine’s CNC routers, manufacturers can produce life rafts that are lightweight, durable, and ready for life-saving deployment, enhancing maritime safety.
The Power of CNC Technology in Maritime Manufacturing
Why CNC Machinery is a Game-Changer
CNC machinery has revolutionized maritime manufacturing by delivering precision, scalability, and efficiency. Unlike manual methods, CNC systems automate repetitive tasks, reduce human error, and handle complex designs with ease. For components like propellers, rudders, anchors, and life rafts, this results in:
- Tighter Tolerances: Achieving tolerances as low as 0.001 inches ensures components fit perfectly and perform optimally.
- Material Versatility: CNC machines process metals, composites, and polymers, accommodating diverse maritime applications.
- Sustainability: Precise cutting minimizes material waste, supporting eco-friendly manufacturing practices.
BN Machine’s CNC Solutions
BN Machine offers a comprehensive range of CNC equipment tailored to maritime manufacturing, including:
- 5-Axis CNC Milling Machines: For complex propeller and rudder geometries.
- CNC Routers: For cutting life raft components and shaping rudders.
- Vertical Drilling Machines: For precise anchor hole drilling and component shaping.
- Industry 4.0 Features: IoT sensors and real-time monitoring for predictive maintenance and process optimization.
Our machines integrate seamlessly with CAD/CAM software, streamlining the design-to-production workflow and ensuring accuracy at every stage.
Best Practices for Optimizing CNC Maritime Manufacturing
To maximize the benefits of CNC technology, maritime manufacturers should adopt the following best practices:
- Regular Maintenance: Calibrate CNC machines monthly to maintain precision. Clean spindles, worktables, and coolant systems to prevent debris buildup and ensure smooth operation.
- Operator Training: Invest in training programs to equip staff with skills in CAD/CAM software, machine operation, and troubleshooting, reducing errors and downtime.
- Material Selection: Choose corrosion-resistant materials like stainless steel or bronze for propellers and anchors, and lightweight composites like fiberglass for life rafts.
- Software Optimization: Use advanced CAM software to optimize toolpaths, reducing machining time and tool wear while improving surface finishes.
- Quality Control: Implement automated inspection systems to verify tolerances and detect defects early, ensuring compliance with industry standards.
BN Machine supports clients with comprehensive training, technical support, and maintenance services, helping manufacturers achieve peak CNC performance.
The Future of Maritime Manufacturing with CNC Technology
The maritime industry is undergoing a transformation, driven by trends like automation, sustainability, and digitalization. CNC machinery is at the forefront of this evolution, enabling manufacturers to:
- Embrace Industry 4.0: IoT-enabled CNC machines provide data analytics for predictive maintenance, reducing downtime and optimizing production.
- Enhance Sustainability: Precision machining minimizes material waste and energy consumption, aligning with global sustainability goals.
- Meet Growing Demand: Automated CNC systems scale production to meet the needs of expanding maritime markets, from commercial shipping to offshore energy.
BN Machine is committed to driving this transformation, offering innovative CNC solutions that empower manufacturers to stay competitive in a rapidly evolving industry.
Conclusion
Precision CNC manufacturing is the foundation of high-quality maritime components, ensuring life rafts, propellers, rudders, and anchors perform reliably in the most demanding conditions. By leveraging advanced CNC machinery, manufacturers can achieve unmatched accuracy, efficiency, and scalability, delivering components that enhance vessel safety and performance. At BN Machine, we’re proud to lead the way with our cutting-edge CNC solutions, including 5-axis milling machines, CNC routers, and vertical drilling systems.
Whether you’re producing propellers for fuel-efficient ships, rudders for precise navigation, anchors for unwavering stability, or life rafts for life-saving emergencies, BN Machine has the expertise and technology to elevate your operations. Visit bnmachine to explore our range of CNC equipment or contact our team for a consultation. Together, we can shape the future of maritime manufacturing with precision, reliability, and innovation.