Best Automatic Glass Polishing Machines: 2025 Guide & Reviews
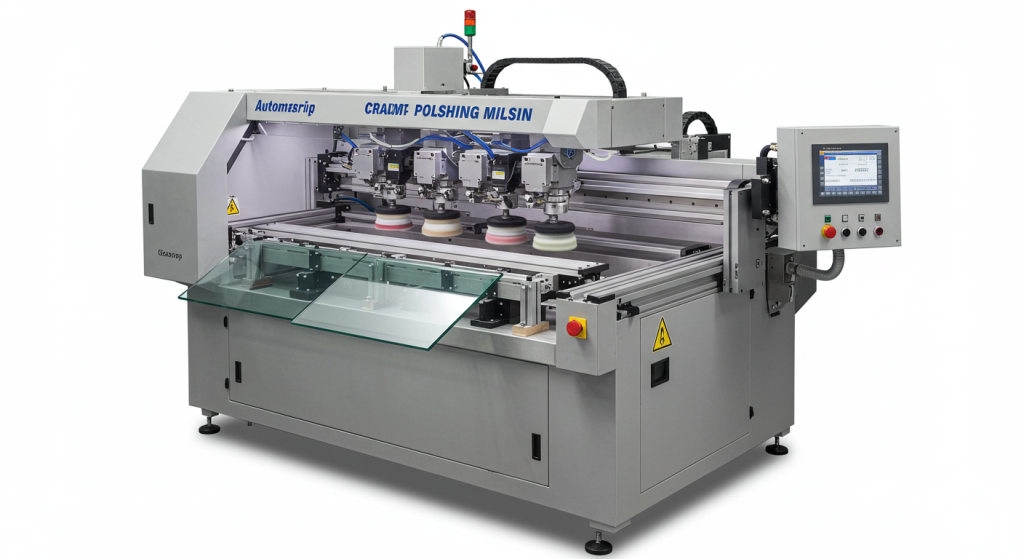
Automatic glass polishing machines are game-changers in the glass processing industry, delivering flawless, high-gloss finishes to glass surfaces and edges with unmatched precision and efficiency. Whether you’re restoring scratched glass, enhancing optical clarity for lenses, or polishing edges for architectural panels, these machines automate complex tasks, saving time and ensuring consistent quality. As industries like construction, automotive, and optics demand superior glass finishes in 2025, automatic polishing machines are essential for staying ahead of the curve.
This comprehensive guide dives into automatic glass polishing machines, exploring their types, key features, applications, benefits, and how to choose the right model for your needs. From small workshops to large-scale fabricators, this article will equip you with the knowledge to invest wisely. Let’s shine a light on your next glass polishing solution!
What is an Automatic Glass Polishing Machine?
An automatic glass polishing machine is advanced equipment designed to polish glass surfaces or edges using automated processes, eliminating the need for labor-intensive manual polishing. These machines employ abrasive wheels, belts, or pads—often diamond, resin, or cerium oxide-based—combined with water-cooling systems to achieve smooth, glossy finishes. They’re used for edge polishing (e.g., flat, pencil, or beveled edges), surface polishing (e.g., scratch removal or frosting), and optical polishing (e.g., for lenses or mirrors).
Equipped with PLC controls, CNC systems, and touchscreen interfaces, these machines ensure precision across glass thicknesses (3-50mm) and sizes (80x80mm to 3000x3000mm). They cater to applications requiring aesthetic appeal, structural integrity, or optical clarity, such as glass doors, tabletops, windshields, and telescope mirrors. Leading brands like Jordon Glass Machinery, Zafferani, and Glaston offer models with 6-15 spindles for edge polishing or specialized pads for surface restoration, making them versatile for diverse industries.
Types of Automatic Glass Polishing Machines
Automatic glass polishing machines vary by function and design, addressing specific polishing needs. Here’s a breakdown of the main types:
Automatic Edge Polishing Machines
These machines focus on grinding and polishing glass edges to create flat, pencil, beveled, or arris finishes. Models like the Jordon DZM9 (9 spindles) or Guangzhou Huatian’s 6-spindle machine process glass from 3mm to 20mm thick, using diamond wheels for grinding and cerium wheels for high-gloss polishing. They’re ideal for architectural glass, furniture, and mirrors.
Double-Edging Polishing Machines
Double-edgers, such as LIJIANG Glass’s LGZM3525, polish two opposing edges simultaneously, doubling efficiency for high-volume production. They handle large panels (up to 3000mm wide) for construction or furniture, integrating arris grinding and Low-E film deletion for energy-efficient glass.
Surface Polishing Machines
Surface polishers restore scratched glass or enhance clarity, often using felt pads and cerium oxide slurries. Glaston’s machines, designed for automotive or architectural glass, remove light scratches and blemishes, achieving optical-quality finishes. They’re perfect for refurbishing windows or windshields.
Optical Polishing Machines
Specialized for lenses, telescope mirrors, or precision optics, these machines use ultra-fine abrasives and CNC-controlled pads to achieve sub-micron surface smoothness. They’re used in aerospace, medical, and scientific applications, where clarity and precision are critical.
Vertical Polishing Machines
Vertical models, like Matodi’s Neptun edgers, save space and polish edges or surfaces upright, handling glass up to 7/8” thick. They’re suited for small to medium workshops, offering flexibility for flat or mitered edges with 6-12 spindles.
Each type targets specific applications, with spindle counts (6-15) or pad types determining precision and speed. Choose based on whether you prioritize edge, surface, or optical polishing.
Key Features to Look for in an Automatic Glass Polishing Machine
Selecting the right machine depends on features that enhance performance, versatility, and ease of use. Here’s what to prioritize:
- Polishing Mechanism: Edge polishers need 6-15 spindles with diamond, resin, and cerium wheels; surface polishers require felt pads or belts with adjustable pressure for scratch removal.
- Automation and Controls: PLC systems (Mitsubishi, Siemens) and CNC integration ensure precise settings for speed, pressure, and polishing patterns, reducing errors.
- Conveyor System: Ball-bearing or timing belt conveyors handle glass from 80x80mm to 3000x3000mm, supporting loads up to 2000lbs for stable processing.
- Cooling System: Water jets or slurry delivery systems cool abrasives and remove glass dust, ensuring clean finishes and prolonging tool life.
- Adjustability: Machines should accommodate glass thicknesses (3-50mm), edge types (flat, bevel, pencil), or surface finishes (frosted, glossy) with quick setups.
- Durability: Monolithic steel frames, anti-corrosion coatings, and components from Schneider Electric or Omron ensure long-term reliability.
- Safety Features: Emergency stops, sealed cabins, and dust extraction systems protect operators, meeting CE standards.
- Tool Versatility: Compatibility with multiple abrasives (e.g., cerium oxide, aluminum oxide) and tools (wheels, pads, belts) enhances flexibility.
These features ensure a machine that’s efficient, safe, and adaptable to your polishing needs.
Applications of Automatic Glass Polishing Machines
Automatic glass polishing machines serve diverse industries, delivering functional and aesthetic results:
- Architectural Glass: Polished edges for windows, balustrades, and shower enclosures enhance safety and elegance, while surface polishing restores scratched panels.
- Furniture: Glossy edges or frosted surfaces on tabletops, shelves, and cabinet doors elevate modern interiors.
- Automotive: Edge polishing for windshields and side windows ensures durability, while surface polishing removes scratches from used vehicles.
- Optics and Aerospace: Optical polishing for lenses, telescope mirrors, and aircraft glazing achieves sub-micron clarity for precision applications.
- Mirrors and Decorative Glass: Beveled edges or frosted patterns on mirrors and art pieces add sophistication to homes and businesses.
- Electronics: Polishing glass for smartphone screens or touch panels ensures clarity and scratch resistance.
These applications highlight the machines’ versatility in meeting both industrial and artistic demands.
Benefits of Using Automatic Glass Polishing Machines
Investing in an automatic glass polishing machine offers significant advantages:
- High Efficiency: Automation via PLC/CNC systems processes glass at speeds up to 3000mm/min, reducing labor and boosting throughput.
- Superior Finish: Consistent, scratch-free edges or surfaces meet stringent quality standards, enhancing client satisfaction.
- Versatility: Handle edge, surface, or optical polishing across glass types (tempered, laminated, float) and sizes in one system.
- Safety: Polished edges eliminate sharp surfaces, while surface restoration extends glass lifespan, reducing replacement costs.
- Cost Savings: Automated processes lower labor costs, and durable tools (e.g., diamond wheels) minimize maintenance expenses.
- Precision: CNC controls ensure repeatable results, critical for optics or large-scale production.
A fabricator using a Glaston surface polisher noted, “We restored 50 scratched windows in a day, saving clients thousands in replacements.” These benefits make automatic polishers a strategic investment.
How to Choose the Right Automatic Glass Polishing Machine
Selecting the best machine requires aligning its capabilities with your needs:
- Polishing Needs: Choose edge polishers (e.g., Jordon DZM9) for architectural glass, surface polishers (e.g., Glaston) for restoration, or optical polishers for precision optics.
- Production Volume: Small shops can opt for 6-spindle vertical models; large fabricators need 12-15 spindle or double-edgers for high output.
- Glass Specifications: Ensure compatibility with your glass sizes (80x80mm to 3000x3000mm) and thicknesses (3-50mm).
- Budget: Entry-level machines cost $8,000-$20,000; high-end optical or double-edgers range from $50,000-$500,000. Used options from Matodi save costs.
- Space Constraints: Vertical machines (e.g., 6400x1200x2500mm) suit small spaces; horizontal systems need larger areas.
- Brand and Support: Choose brands like Zafferani, Jordon, or Glaston with reliable service and spare parts availability.
- Maintenance: Opt for machines with accessible wheels/pads and clear manuals to minimize downtime.
A comparison table of polishing type, spindle count, and glass size can streamline your decision-making process.
Top Brands and Models of Automatic Glass Polishing Machines
Leading brands offer reliable models for various polishing tasks:
- Jordon Glass Machinery: The DZM9 (9 spindles) and DZM12 (12 spindles) excel in edge polishing; the DS1 handles shapes for mirrors.
- Guangzhou Huatian: Their 6-spindle edge polisher is budget-friendly for small shops, processing 3-20mm glass at 500-3000mm/min.
- Zafferani: The 8-spindle flat glass polisher delivers precise edge finishes for furniture and architecture.
- Glaston: Specializes in surface polishing for automotive and architectural glass, ideal for scratch removal.
- LIJIANG Glass: The LGZM3525 double-edge line integrates polishing and film deletion for Low-E glass.
- Matodi (Neptun): Italian vertical edgers for edge polishing, compact and durable for medium operations.
Compare models by polishing type, automation, and glass capacity to find the best fit.
Maintenance and Safety Tips for Automatic Glass Polishing Machines
Proper care and safety practices ensure machine longevity and operator protection:
- Maintenance:
- Clean water jets and slurry troughs daily to prevent clogs and corrosion.
- Inspect wheels, pads, or belts monthly, replacing worn ones to maintain finish quality.
- Lubricate spindles, bearings, and conveyors per manufacturer guidelines to reduce wear.
- Safety:
- Wear gloves, goggles, and masks to protect against glass dust and slurry splashes.
- Ensure electrical components (e.g., Siemens, Omron) are grounded to prevent shocks.
- Train operators on PLC/CNC controls and emergency stops for safe operation.
- Troubleshooting:
- Hazy surfaces? Adjust cerium slurry concentration or pad pressure.
- Conveyor slippage? Check belt tension or bearing alignment.
Adhering to CE standards and using a maintenance checklist minimizes risks and downtime.
Cost Considerations and ROI
Costs for automatic glass polishing machines vary by type and features:
- Cost Range: Entry-level edge polishers start at $8,000-$20,000; surface or optical polishers range from $50,000-$500,000.
- Cost Factors: Spindle count, automation (PLC/CNC), and specialized features (e.g., optical polishing pads) drive prices.
- ROI Benefits:
- High-speed processing (up to 3000mm/min) reduces labor costs and boosts output.
- Premium finishes attract high-value clients, increasing revenue.
- Restoration capabilities extend glass lifespan, saving replacement costs.
- Used vs. New: Pre-owned machines from Jordon or Glaston can save 20-40%, though maintenance costs may be higher.
Financing options from suppliers like Matodi make high-end models accessible. Contact suppliers for accurate quotes, as prices vary by region.
Common FAQs About Automatic Glass Polishing Machines
- Can these machines polish both edges and surfaces? Some models (e.g., multi-function edgers) handle both; others are specialized for edges or surfaces.
- What abrasives are used? Diamond and resin wheels for edges; cerium oxide pads or slurries for surfaces.
- How fast are they? Edge polishers process at 500-3000mm/min; surface polishers vary by area and finish.
- Are they suitable for small shops? Vertical or 6-spindle models are compact and cost-effective for smaller operations.
- Is training required? Basic training for PLC/CNC systems ensures safe and efficient use.
These answers address common queries, boosting engagement and SEO.
Conclusion
Automatic glass polishing machines are essential for achieving flawless edges and surfaces, from architectural glass to precision optics. Their automation, versatility, and precision make them invaluable for small studios and large fabricators alike. By understanding their types, features, and applications, you can select a machine that enhances productivity and quality in 2025.
Ready to elevate your glass finishing? Explore top models from BNMACHINE Glass Machinery, Glaston, or LIJIANG Glass, and contact suppliers for quotes. Share your questions or project ideas in the comments—we’re excited to hear about your polishing journey!